APPRO PRIMX PROJECTS
AT A GLANCE
Project Size:
Project #1: 156,000 sf
Project #2: 286,000 sf
Project #3: 185,000 sf
Date:
Project #1: 2015
Project #2: 2017
Project #3: 2020
Location:
All projects: Lakeville, MN
“This floor is now six years old and looks like the day we poured it. It’s held up very, very well in an abusive environment.”
Jack Matakosky
Owner & CEO
Appro Development
HEAVY DEMANDS & DAILY ABUSE
A heavy custom metal fabricator needed a floor that wouldperform under daily abuse. The visionaries at ApproDevelopment determined PrīmX was the answer.
Six years ago, Jack Matasosky, Owner & CEO of Appro Development, had a client with a very specific request: construct a facility for heavy custom metal fabrication with floors that can withstand ongoing abuse. The client had experienced issues with floors in each of their facilities and was eager to find something new.
At the time, PrīmX was just introduced to the North American market. In fact, there was only one floor in North America placed 20 miles away in the Minneapolis-St. Paul, MN Metro. Jack and his client checked it out, performed due diligence on floors installed in Europe, and ultimately made the decision to choose PrīmX.
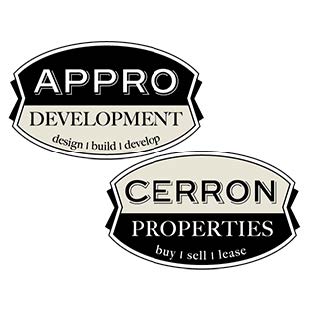
The Evaluation
According to Jack, the two most important components of any industrial building are the roof and floors. For this client, the floors were #1. Daily use at the custom metal fabricator involved heavy metal racking and non-stop, wire-guided fork truck traffic carrying massive loads of steel. Flatness mattered as well, with very specific parameters required to optimize the wire-guided system.
Based on the loads and traffic anticipated in the facility, the engineer on the project specified traditional concrete floors with thicknesses varying from 8” to 12”, all with a double mat of rebar. The floors would be saw cut every 12’, as traditional concrete requires. Fillers were also required in the miles of joints created by saw-cutting.
The PrīmX engineers reviewed the project plan & floor requirements as well, designing a 6” PrīmX floor with no saw-cuts, no joint fillers, no rebar, and load capacities greater than the traditional concrete design. In addition, the floor would meet/exceed the strict flatness requirements. And the best part? The superior PrīmX option was a cost-savings over the original design
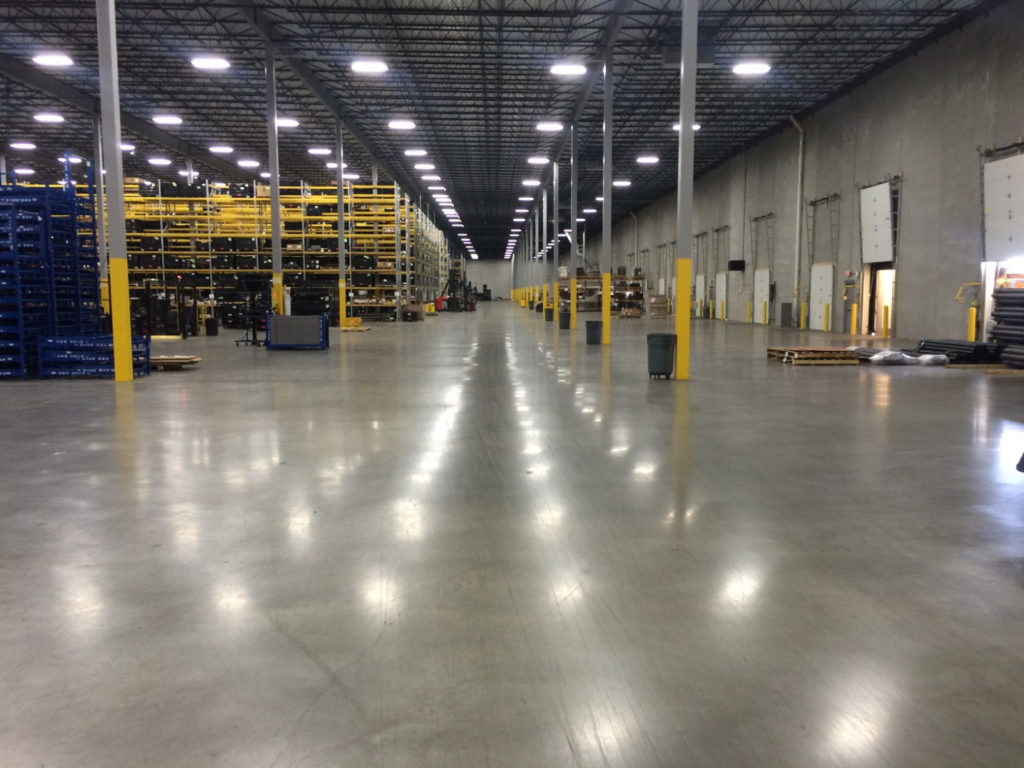
The Result
The team at Appro worked with PrīmX Licensee, Gresser Companies, on the construction. Although the process was very similar to any industrial build that they were accustomed to, there were a couple extra steps.
“With a PrīmX floor, the process was very similar,” Jack shared. “However, the team at Gresser performed extensive testing on the local aggregates & cements, as well as suitability of the sub-soils. Although the testing was more than what we were used to, it was honestly appreciated and produced a terrific result.”
Once placed, testing was conducted to ensure the floor was within tolerances specified for the wire-guided fork trucks. The tests proved the floor’s flatness, with no additional grinding or preparation needed.
Repeat Customer
Since the first project six years ago, Appro Development and its clients have installed over 600,000 square feet of PrīmX in three different facilities.
A self-declared “strong advocate” of PrīmX, Jack believes it is a great fit for heavy industrial uses like his metal fabrication client.
“This floor is now six years old and looks like the day we poured it,” Jack said. “It’s held up very, very well in an abusive environment.”
With more projects coming up, the team at Appro is evaluating the intended use and occupant of each project, knowing that PrīmX is the best when client needs are demanding.