WHY PrīmX
With PrīmX you get jointless, saw-cut free industrial concrete floors. With no joints and 50% stronger concrete that doesn’t require rebar placements, you can reduce construction time by upwards of 30%. In addition, the lack of rebar and flatness of PrimX means that you have more flexibility in racking and lower repair and maintenance costs to both the floor and forklifts or your AGVs. Finally, thanks to the strength and design of PrimX, you can reduce CO2 emissions by up to 70% vs. and qualify for LEED credits. PrīmX jointless industrial floors are proven globally — and taking off in North America. Don’t sacrifice the performance and quality of your construction with second-rate concrete.
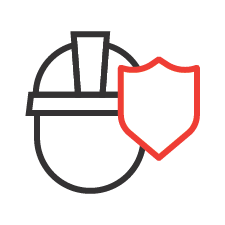
Built for Safety
According to OSHA, approximately 95,000 U.S. warehouse workers are injured every year while operating forklifts. Back injuries, often developed from repeated strain while driving machinery over joints, is the leading injury type. Not only are joints rough on machinery and employees’ backs, and they can harbor contaminants that taint the air and products. There are no joints in a daily pour of PrīmX floors—eliminating a mile or more per typical placement. Construction joints remain tight, and unlike other extended joint systems, there are no dominant joints on a PrīmX floor. No joints mean you can provide a safer, smoother, and quieter environment for workers.
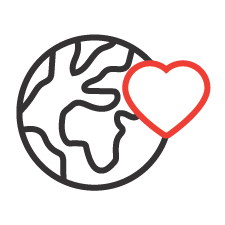
Built for the Environment
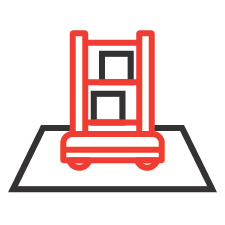
Built for Automation and Flexibility
Automation is the future of warehousing, industrial and manufacturing operations. With a smoother and flatter floor than traditional concrete, robotics can navigate the space with no disturbance from curled joints and open cracks. Flatter floors and no rebar also mean you get increased facility flexibility with no limitation on racking placement. PrimX delivers longer-lasting floors that require less maintenance on both the floor and the automated vehicles that operate on it.
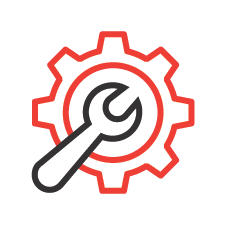
Lower Maintenance Costs, Longer Floor Life
Most traditional concrete floors require costly maintenance and repairs to fix curling throughout miles of joints. Machinery subjected to traditional concrete floor joints take daily abuse and result in higher maintenance costs. With PrīmX, those issues disappear. Floors don’t shrink or curl and can be cleaned using the same process used to clean traditional concrete floors.
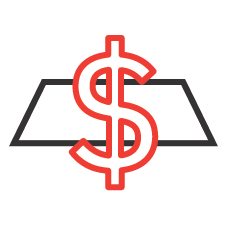
Better Bottom Line,
Faster Construction
So what do you lose when choosing PrimX?
You lose weeks of construction time, miles of rebar, miles of joint sealants, saw cutting, and all the hazards associated with silica dust created by saw cutting. You gain faster projects and fewer delays.
SEE OUR CONCRETE IN ACTION
Watch this 30 sec time lapse
Explore how PrīmX can elevate your project